Machine Vision
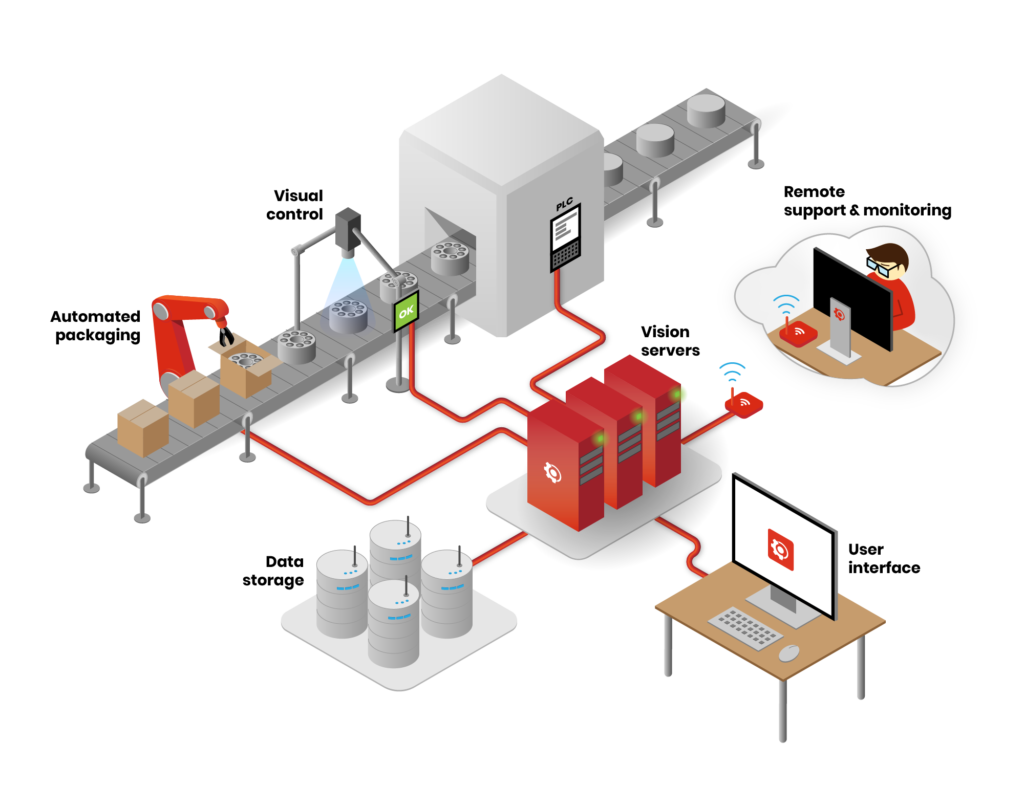
Vision Inspection Systems
Machine Vision systems are low-cost, high-performance online inspection devices that are used to automatically measure parts, verify the correct assembly applications, form verifying print quality, location, and position to deciphering 1-D and 2-D barcodes.
Machine Vision systems help to reduce the human error element on the factory floor. They increase efficiency by providing real time production data for SPC package to provide trending and warn/fail conditions. In order to have 100 percent accurate inspection, it is critical that the installation have proper lighting, lenses, and professional programming.
Machine vision system inspection consists of narrowly defined tasks such as counting objects on a conveyor, reading serial numbers, and searching for surface defects. Manufacturers often prefer machine vision systems for visual inspections that require high speed, high magnification, around-the-clock operation, and/or repeatability of measurements.
Machine vision systems inspect silicon wafers, processor chips, and sub-components such as resistors and capacitors at high speeds with precision and accuracy.
Our Company has dedicated itself to vision by making a long-term commitment to obtaining these results. With a Machine Systems from Firstcall automation, manufacturing has a flexible tool that improves productivity; ensure quality production of a part, increase efficiency, and lower production costs.
Application:
- Defect detection
- Gauging – Measuring
- Presence/absence detection
- ID Reading
- Character reading and verification
- Color matching and verification
- Texture and material classification
- Integrated Robotic Control.